hardness test on nitride coating|best hardness testing methods : bespoke Determining nitriding hardness depth to DIN 50190-3. The determination of nitriding hardness depth is described in the DIN 50190-3 standard. This is ascertained from the hardness curve and lies at a hardness limit of 50 HV . 10 de jan. de 2024 · Plants vs. Zombies™ 9+. Electronic Arts. “动作”类第 23 名. 4.8 • 71.1万 个评分. 免费. 提供 App 内购买项目. iPhone 截屏. Get ready to soil your plants as a mob of fun-loving zombies is about to invade your home.
{plog:ftitle_list}
webNovinhos da imperium. 29 videos. Novinhosdaimperium. 102 videos. Favorites. 144 videos. Amador . 29 videos. Nayra e Luan . Recent porn videos by Jahdkkdkfk. 31m 4k. Peituda. 5.8K 98% 1 year . 74m 1080p. . Casada e safada da kally da pra negão na barbearia goza no pal dele de.. 86K 94% 4 years . 54m. Married realizes fantasy of being .
Hardness testing can be a quick and effective tool for checking coating properties, especially in high volume production environments. However, selection of an appropriate approach and understanding key advantages and .

Nitrided cases are very hard at the surface but the hardness tends to fall off very quickly thru the case depth. If all you want is a surface hardness, your Vickers tester should .How to use the Brinell hardness test for large samples with a coarse or inhomogeneous grain structure.
The Brinell hardness test involves indenting a material with a hard sphere under a specific load. Two diameters (x and y axis) of the indentation are measured, and the hardness value is .
Determining nitriding hardness depth to DIN 50190-3. The determination of nitriding hardness depth is described in the DIN 50190-3 standard. This is ascertained from the hardness curve and lies at a hardness limit of 50 HV . We can achieve a final surface hardness of up to 76 HRC (90 HRA) through the nitriding process. The hardness layer (case depth) generally has a thickness of 200–300 𝜇m (0.0002m) but can be up to 2 mm in some .Nitriding is a surface hardening technique that involves diffusing nitrogen into the surface of ferrous materials, such as steel and iron. This process forms a hard, wear-resistant nitride layer on the component's surface, improving its overall .
the hardness increases with increasing con-tent of nitride forming alloying elements, at the same time the case depth decreases. Nitrided carbon steels have a surface hard-ness of 300-400 .Gas Nitriding is a low temperature diffusion hardening process known for fatigue-resistance, corrosion-resistance, anti-galling, and lowered coefficient of friction. The process is suitable for . When you nitride a steel part, it can become significantly harder, typically by 200-1000 HV (Vickers hardness), depending on the type of nitriding process used and the steel composition. The depth of the nitride layer also .
Plasma nitriding/Ion nitriding. Plasma nitriding (Ion nitriding) is a plasma supported thermochemical case hardening process used to increase wear resistance, surface hardness and fatigue by generation of a hard layer including compressive stresses.The unique combination of a thin hard coating with a thicker, strengthened supporting layer is characteristic only for nitrided cases. . This is clearly depicted in Figure 42 on the example of the influence of the test temperature on the hot hardness. The thermal stability legitimates the application of nitrided components, e.g., nitrided hot . Introduced to the global market in the 1970s, thin films based on the transition metal nitrides are one of the first commercially applied anti-wear coatings [1].Their undiminished popularity results from the exceptional properties of the nitride-based films: high hardness, chemical stability, good corrosion performance, high melting point and good electrical . Transition metal nitride (TMN) films with excellent hardness and lubricating performance are versatile low dimension materials, which are widely used in various fields including industries, transportation, aerospace, and so on. This paper introduces one film design strategy and provides a review of the mechanisms for strengthening and lubricating nitride .
Titanium nitride (TiN) coating is wear resistant, inert and reduces friction. Use it on cutting tools, punches, dies and injection mold components to improve tool life two to ten times, or more, over uncoated tools. . Hardness: 2400 – 2600 Hv (>80 Rc). This Vickers Hardness correlates to a hardness considerably above 80 Rc. (Rockwell C is .nium-based nitride coatings including TiN, TiAlN, and TiAlCrN were, respectively, deposited on the surface of high-speed steel substrate W 6Mo 5Cr 4V 2 (M2) by the phy-sical vapor deposition technology. The hardness test, scratch test, Rockwell adhesion test, and pin -on-disc (POD) wear test were carried out aiming to investigate the per-
what is hardness testing
A hardness level of 19 GPa was reached for a metal coating based on the TiZrNbTaHfCr alloy, 63 GPa for a nitride coating based on the TiZrNbVHf alloy, and 48 GPa for a carbide coating based on the TiZrNbVHfTa alloy. The analysis showed that nitride coatings were the hardest, while the lowest friction coefficient was possessed by oxide coatings.In this work, the titanium-based nitride coatings including TiN, TiAlN, and TiAlCrN were, respectively, deposited on the surface of high-speed steel substrate W 6 Mo 5 Cr 4 V 2 (M2) by the physical vapor deposition technology. . The hardness test, scratch test, Rockwell adhesion test, and pin-on-disc (POD) wear test were carried out aiming to . The layer thickness was 5 -12 microns with an average hardness of 900HV. Fluidised bed nitriding (Nobleizing) equipment, currently able to handle larger parts up to 750mm diameter produces thicker films without risk of spalling or cracking. Hardness levels above 650HV are reported for titanium. Problems Associated with Nitride CoatingsThe determination of nitriding hardness depth is described in the DIN 50190-3 standard. This is ascertained from the hardness curve and lies at a hardness limit of 50 HV above the core hardness, see illustration (NHD).The surface of the specimen on which the measurement is performed must be finely machined.
isid compression test
Because of their great hardness, titanium nitride (TiN) coatings are widely utilized to improve the wear qualities of many parts. Chemical Vapor Deposition (CVD), Physical Vapor Deposition (PVD), and Physical Vapor Deposition (PACVD) are some of the coating processes that can be utilized to deposit material on a surface (Plasma-Assisted . Aluminium nitride (AlN) coating has attained the utmost interest for its wide applications, like semiconductors, optoelectronics, aerospace, defence, crucibles and vessels for handling corrosive chemicals, etc. [1], [2].This wide applicability of AlN is the consequence of its excellent physical and chemical stability even at fairly high temperature, low coefficient of .
However, traditional hardness testing yields only one measure of deformation at one applied force, whereas during an IIT test, . titanium-nitride coating that is gold in color, and this coating extends onto the main body of the blade, as shown in Figure 2.
islg compression test
industrial hardness testing
This process forms a hard, wear-resistant nitride layer on the component's surface, improving its overall performance and durability in various applications. Benefits and Advantages of Nitriding. Nitriding offers numerous benefits, including: Improved wear resistance; Increased surface hardness; Reduced friction and galling In the present work, hardness and elastic modulus of a titanium nitride coatings prepared on Ti6Al4V by powder immersion reaction-assisted coating (PIRAC) are tested and comparatively studied with .Titanium nitride (TiN; sometimes known as tinite) is an extremely hard ceramic material, often used as a physical vapor deposition (PVD) coating on titanium alloys, steel, carbide, and aluminium components to improve the substrate's .
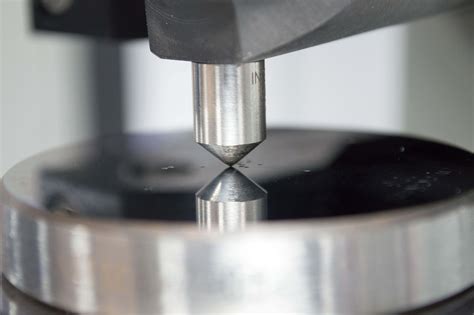
Coatings with low nitrogen content (~6 at. %) exhibit a fcc structure, offering the best scratch toughness and adhesion strength, but inferior hardness (~11 GPa) and wear resistance; coatings with .
The combination of high hardness, excellent wear resistance, corrosion resistance and inertness makes titanium nitride (TiN) an ideal protective coating for metal components in various industries.Chromium nitride coatings were deposited on EN-24 steel substrates with reactive DC magnetron sputtering. The argon flow rate was 30 sccm, while the nitrogen flow rate was set at 10 sccm, and the samples . N phase causes increasing in the hardness of the coating. The wear test showed the COF of 0.39 and wear is 30 micron for the coating . The test results showed that the AlCrN coatings deposited under nitrogen pressure in the range from 1 to 5 Pa show similar hardness for all the coatings, which is around 17 GPa. The increase in the negative bias voltage of the substrate during the formation of the coating deteriorates its adhesion to the substrate, although the wear rate is .
Titanium nitride coatings were deposited on three Ti beams under three conditions. Two of the Ti beams were coated at 300 °C and 2 mTorr nitrogen/Ar ambient for two different times of 1.5 h and 3 h. . Nanoindentation is an ideal hardness test for thin films because low indentation depths can be achieved using a nano-sized diamond tip. The .
The development of advanced materials and construction of multilayer structure contribute to enhancing the performance of protective coatings, further improving the industrial productivity and conserving energy. In this paper, the self-assembled high-entropy nitride (HEN) AlCrNbSiTiN multilayer coating was designed by harnessing the plasma distribution .Titanium Nitride. Valentina К. Prokudina, in Concise Encyclopedia of Self-Propagating High-Temperature Synthesis, 2017. Abstract. Titanium nitride is a refractory compound with high microhardness and chemical and thermal stability. TiN has a variety of applications: as a component in special refractories and cermets, as a material for crucibles for anoxic casting of .
The nano-hardness and modulus of elasticity of the untreated TA2 pure titanium were 3.53 and 136.27 GPa, respectively. The hardness value of nitrided layer and coatings was 16.5–24.7 GPa and 20.0~ 26.3 GPa, respectively. The present article explores the ability of synthesized graphene carbon nitride (g-C 3 N 4) towards the improvement of microstructure, surface energy, surface hardness, and scratch resistance of electroless nickel phosphorus-graphene carbon nitride (NiP/g-C 3 N 4) coated AISI 4140 steel.Comparative studies were conducted to evaluate how the g-C 3 N 4 . This paper experimentally examines the influence of coating thickness, test temperature, coating hardness, and defects on the erosion resistance of boride coatings, ion plating CrN coatings, and thermal spraying coatings. The results demonstrate that the erosion rate of coating can be reduced effectively by improving coating hardness and thickness with .Physical Properties Chromium Nitride (CrN) PVD Coatings; Composition: CrN. > 99 % purity. Process: PVD Vacuum Deposited Coating. . Hardness, H: Hardness > 1500 kg/mm2 Knoop or Vickers Microhardness. Values of 2000-2500 are typical. . Several adhesion test methods are possible, contact BryCoat for more info. Adhesion, Scratch Adhesion Value .
hardness testing of paints

WEB26 de out. de 2016 · FMEA (Failure Mode and Effect Analysis)的基本理念. 对失效的产品进行分析,找出零组件之失效模式,鉴定出它的失效原因,研究该项失效模式对系统会产生什么影响。. 失效分析找出零组件或系统的潜在弱点,提供设計、制造、品保等单位而采取可行之对策。. 何谓FMEA .
hardness test on nitride coating|best hardness testing methods